基于精益生產理論的DH公司生產過程搬運浪費問題思考
時間:2022-06-04 來源:51mbalunwen.com作者:vicky
本文是一篇生產管理論文,筆者認為精益生產理論中,搬運浪費之外的其他浪費也是時刻存在的,DH 公司應該加大在其他浪費方面的改善力度。在精益生產理論的指導下將九大生產浪費逐步消除,這樣的結果必將是給企業帶來更大的效益。無論是對企業的產品戰略還是將產品的完全生命周內的各個階段做到極致,更加能促進企業內部的向心力凝聚。
第一章 緒論
第一節 研究背景
在現代制造業的生產過程中,生產浪費問題同產品質量問題一樣,伴隨著生產活動的開展而不斷產生,難以根本消除。時至今日,眾多國內外企業管理層以及相關專家學者仍然希望能夠通過不斷創新生產,改善管理來解決生產浪費這一難題。據相關研究表明,浪費相對嚴重的企業可能存在一半以上的生產成本均由各種浪費造成。尤其是一些生產管理相對薄弱的傳統制造業企業,浪費所造成的成本更是占據了生產成本的很大比重。降低生產成本,減少各種浪費則成了生產性企業當務之急中的重中之重。
日本豐田公司作為最早起步施行精益生產方式的標桿企業,更是把生產過程中的各種浪費行為歸結成了八大類:制造過剩、庫存、搬運、加工、動作、等待、不良品、能動性(未能發揮員工積極主動性的浪費)[1]。除此之外,管理浪費也應當被納入其中,這種浪費表現在企業內部管理無序,執行力弱等情形上。管理浪費的存在是存在于絕大部分企業的一種普遍現象,企業往往需要花費大量人力物力的投入才能盡可能的改善和避免這種隱性的等待浪費。但較之于關注和改善浪費行為能夠為企業帶來的可觀收益,減少各種浪費也就理所當然成為了生產性企業增加生產收益、提升企業利潤、實現戰略目標的重點工作內容。
目前來看這些浪費問題存在于幾乎所有生產性企業當中。正如精益專家大野耐一先生所述——“減少 10%的浪費就相當于增加 100%的銷售額”,這句話正是明確闡明了減少制造業企業生產過程中的浪費問題是提升企業盈利空間的重要途徑。
DH 公司是一家位于中部省份的一家小型農用機械生產企業。公司成立于2008 年,隨著公司規模的不斷擴大和生產研發能力的逐步提升,公司的主營內容已經從最初的簡單的整機組裝轉變到現在基本實現完全自主生產。DH 公司的產品在國內外小型農機市場中以“質量過硬,價格公道,服務至上”的尚佳用戶口碑廣受全國各個地區客戶青睞,目前每年的銷售量穩定保持在 5 萬臺以上并逐漸擴增,自公司開展銷售以來已經先后服務三十萬以上客戶。
第二節 研究目的和研究意義
一、研究目的
就 DH 公司而言,日益增加的產品銷售數量和隨之增加的服務客戶數目都勢必要求 DH 公司在產品生產制造和產品售后方面相關方面增加資金投入,而在總體資金受到制約的情況下,公司就不得不考慮將利潤增長點放在了“節流”上面。而生存發展了 13 年之久的 DH 公司的生產規模也是一步步地在擴大,原有的陳舊生產規劃相對滯后,在制品的搬運浪費現象也日益突出,這也阻礙了公司生產效率的提升。同時,類似于等待浪費等浪費現象也一直始終充斥于生產的全過程之中,生產部每天的全員班前會占用時間基本為 15 到 20 分鐘,會后要想進入生產狀態,各工位的準備時間等又需要 20 分鐘以上,最長的時候準備時間長達 45分鐘。往往生產進入有序狀態,基本上需要上班后將近 1 個小時。每個生產班組八分之一的時間就這樣被白白浪費掉。為長期持久地生存發展下去,并使效益增加,減少在生產過程中各種浪費也就日趨重要。
以 DH 公司眾多產品中的一款自制件 750 鋤草輪為例進行說明,該自制件的銷售價格為 100 元,其總成本核定為 90 元,單件利潤僅為 10 元。想要實現利潤翻倍的目標有兩條實現途徑:一是在不進行生產過程優化和改善的前提下,產品單件利潤不變,只有通過將該產品的銷售量翻倍的方式來實現利潤翻倍。眾所周知,這樣的目標達成難以企及且需要投入大量營銷費用。二是將目前生產產品的總成本壓縮 10 元,通過關注和減少生產過程中的浪費問題來壓縮成本、提升產品利潤就要相對容易的多。因此,對 DH 公司生產過程中各種浪費問題進行研究及改善是毫無疑問具有其現實意義,也能夠為行業內其他企業借鑒意義,促進行業發展。通過對 DH 公司搬運浪費問題進行研究和實踐,筆者一方面能夠幫供職企業 DH 公司制定企業更合理的生產改進方案,另一方面能夠將研究所學理論聯系實踐、總結經驗后形成系統教學教材以供新進員工系統培訓使用,也可以在未來作為企業的生產指導體系核心內容長期運用。
第二章 相關理論及概念
第一節 精益生產的理論基礎
一、精益生產的來源
生產方式的相關理論大體上分為三種:第一種是泰勒的科學管理理論;第二種是戴明的質量管理理論;第三種是精益生產理論。精益生產理論起源于二戰后。美國福特汽車依靠其資源豐富、大量資金投入、大規模場地,采用批量生產模式——品種少且依托規模化而降低成本,提高競爭優勢。僅在 1949 年,美國福特單日產量達到 7000 臺,相當于日本豐田建廠之后總產量的近 3 倍。
日本的豐田汽車公司面臨著國內資源匱乏、技術落后、可用場地小等諸多困難。在豐田競爭優勢長期不足的情況下,由大野耐一建立了一套適合日本戰后基本國情的豐田管理模式,通過“一人多機”、“目視化管理”等管理方式,使豐田扭虧為盈,形成了豐田準時化生產 JIT(Just In Time)。之后被美國麻省理工學院(MIT)的教授詹姆斯.P.沃麥克總結為精益生產(Lean Production)。豐田汽車公司利用 JIT 使豐田汽車的年產量在 2014 年達到了 998 萬輛,位列當時的世界第一。
二、精益生產的概念及特征
精益生產方式是一種區別于單品種、大批量生產方式的小型化,多品種,多樣化的生產方式。與大批量生產方式相比較,精益生產方式具有準時化生產(JIT),看板管理,員工參與度高等特點。在《改變世界的機器》一書中,丹尼爾教授給精益生產定義了 5 個方面的特征:
(1)把用戶當“上帝”。 (2)以“員工”為中心,適當放權,充分發揮員工的積極主動性。 (3)精簡組織機構,盡可能多采用 JIT 和看板式管理物流,大量降低在制品和產成品庫存,減少廠內物流。 (4)培養團隊意識和并行設計。 (5)及時化準時化供貨方式。降低在制品和產成品庫存量,減少搬運頻率和廠內物流車流動頻次。
第二節 生產浪費的分類及搬運浪費定義
一、精益生產理論中生產浪費的概念及分類
企業在生產經營中活動中,不增值活動的占比最高能達到 90%以上。這就意味著只要企業正常生產運營,就會不停地發生不增值活動,而有一些不增值活動也是企業運營過程中必然會出現的[1]。 精益生產理論認為:不增值活動可以分為可以不做的作業和不得不做的作業兩種:
(1)可以不做的作業,即只增加成本而不產生附加值的活動。它們約占企業生產和經營活動 35%,是最先也是最需要改善的活動。例如,尋找、臨時儲存等。
(2)不得不做的作業,是指到目前為止還必須要完成的活動,必須伴隨著生產活動一起實施而不產生附加價值的作業。這一類約占企業生產和經營活動60%。例如,沖壓下料過程中的沖壓模具更換調整維修,機器人操作程序更改微調、為拿取工件工具而產生的走動、拆開包裝物等搬運活動。
精益生產理論認為所有的浪費均為不產生附加值的活動。對于企業來說,無論如何進行生產活動,只要所從事的活動未給企業帶來價值,未給客戶帶來價值的一切活動均能定義為浪費。因此,無論是庫存的在制品還是產成品,亦或者是呆滯品;無論是再小的瑕疵還是生產過程中可輕易修復的不良;無論是制定戰略的會議還是為了提高效率而開的生產現場會議;無論是為降低成本的計件薪酬還是各種各樣的福利……等等這一切均不會給客戶帶來直接效益,都是精益生產理論中所定義的浪費。
第三章 DH 公司生產過程搬運浪費問題現狀 ...................... 19
第一節 DH 公司的企業概況 .................................. 19
第二節 DH 公司的生產現狀 ..................................... 20
第三節 DH 公司搬運浪費問題現狀 ............................ 21
第四章 DH 公司生產過程搬運浪費問題原因分析及影響 ............. 27
第一節 DH 公司生產過程搬運浪費問題產生的總體原因 ...................... 27
第二節 DH 公司搬運浪費產生的具體原因 ................................ 28
第五章 基于精益生產理論的 DH 公司搬運浪費改善 ................ 35
第一節 生產浪費改善方案 .................................. 35
一、總裝線布局搬運浪費改善方案設計 ............................. 35
二、減速箱分總成分裝線搬運浪費方案設計.............................. 36
第五章 基于精益生產理論的 DH 公司搬運浪費改善
第一節 生產浪費改善方案
精益生產方式的根基是及時化生產(JIT)和消除浪費。面對層出不窮的浪費,要逐一進行消除。針對 DH 公司在生產過程中出現的種種浪費,公司內部也在逐步尋求解決方案,逐個解決。無論哪種原因導致的搬運浪費都是精益生產理論所不允許的。在精益生產理論中,大部分搬運活動都是不增值的活動,都是需要被消除的。限于公司目前實際狀況以及在解決現有浪費的基礎上不再產生新的浪費的情況,DH 公司本著花小錢辦大事的方針正在分批分步驟解決浪費問題。具體的方案本文以搬運浪費中的三個特別例子為對象出設計方案,并擇機實施。
在方案設計機實施過程中,在尊重事實的基礎和最大化效益的原則下,利用ECRS 做改善方案——E(Eliminate)取消,C(Combine)合并,R(Rearrange)重復,S(Simplify)簡化。在此原則之上,將不需要做的搬運流程取消,將能合并的生產線合并或將設備與設備合并在一起,避免一些重復的搬運,簡化生產流程。盡可能多的將所有可以不做的搬運浪費消除。
第六章 結論與展望
第一節 結論
通過對 DH 公司以上幾個具有代表性的零部件和流水線布局調整前后的數據分析對比不難看出,DH 公司在搬運浪費消除方面走出的路是一條積極探索的路。路的方向是正確的,是積極向前的。這三項搬運浪費在整個生產過程中十分突出。要想提高效率,好好節流,消除現有的浪費是一條必由之路。生產過程中的浪費問題在產品生產總成本中的比重之所以最高能達到 95%的最大原因在于,公司管理者習以為常的認為這些很正常,其他企業也是這樣的。這樣的想法直接導致從業者對各種浪費問題的忽略或者重視程度不夠。只有清醒地認識到浪費問題的嚴重程度,進一步通過規劃實施去消除,將消除浪費的 PDCA 不停循環的做下去,浪費問題就會逐步得到解決。
DH 公司僅僅總裝線調整一項消除搬運浪費的直接經濟效益就有六萬元,而這僅僅是基于年產五萬臺的銷量得出的數據。如果 DH 公司年產 10 臺的目標實現,由消除總裝線遷移而導致的搬運浪費所產生的直接經濟效益將翻番。而后期倉庫庫位的調整也將是消除搬運浪費問題的最大最有效途徑。少了搬運,也就省下了部分搬運方面的人力物力支出,同樣也省下了搬運設備方面的財務支出。
從 DH 公司對生產過程中搬運浪費的減少可以看出,浪費的消除或者減少直接的效應除了降低成本,也減少了一線的操作人員。使得 DH 公司向少人化又向前邁進了一步。同樣,生產過程中各種形式浪費的消除將是企業參與市場競爭的一項基本且重要的內功。修煉好此項內功,產品的競爭力必將快速提升。
DH 公司的搬運浪費改善的效果是明顯的,成果也是可值得書寫的。但對比一下改善前不難發現,我們的改善還存在很大的不足:1、還沒有把搬運浪費的改善擴大到公司的其他方面,一些半成品在車間之間的搬運,零件在設備之間的搬運;2、搬運工具的改進不只是行車這一項,升高車以及電動手拉叉車的改進,特別是手動叉車的行進速度上還有很大的空間;3、倉庫在收貨和發貨的過程中登高車的運用上面以及倉庫內庫位設置的不合理等等,4、還沒有將均衡化生產擴大到全部生產線。
參考文獻(略)
第一章 緒論
第一節 研究背景
在現代制造業的生產過程中,生產浪費問題同產品質量問題一樣,伴隨著生產活動的開展而不斷產生,難以根本消除。時至今日,眾多國內外企業管理層以及相關專家學者仍然希望能夠通過不斷創新生產,改善管理來解決生產浪費這一難題。據相關研究表明,浪費相對嚴重的企業可能存在一半以上的生產成本均由各種浪費造成。尤其是一些生產管理相對薄弱的傳統制造業企業,浪費所造成的成本更是占據了生產成本的很大比重。降低生產成本,減少各種浪費則成了生產性企業當務之急中的重中之重。
日本豐田公司作為最早起步施行精益生產方式的標桿企業,更是把生產過程中的各種浪費行為歸結成了八大類:制造過剩、庫存、搬運、加工、動作、等待、不良品、能動性(未能發揮員工積極主動性的浪費)[1]。除此之外,管理浪費也應當被納入其中,這種浪費表現在企業內部管理無序,執行力弱等情形上。管理浪費的存在是存在于絕大部分企業的一種普遍現象,企業往往需要花費大量人力物力的投入才能盡可能的改善和避免這種隱性的等待浪費。但較之于關注和改善浪費行為能夠為企業帶來的可觀收益,減少各種浪費也就理所當然成為了生產性企業增加生產收益、提升企業利潤、實現戰略目標的重點工作內容。
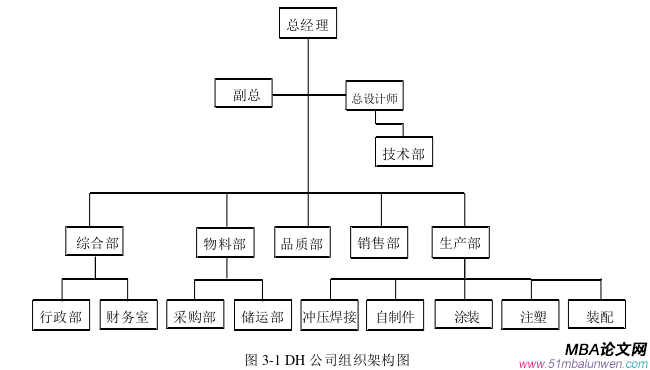
DH 公司是一家位于中部省份的一家小型農用機械生產企業。公司成立于2008 年,隨著公司規模的不斷擴大和生產研發能力的逐步提升,公司的主營內容已經從最初的簡單的整機組裝轉變到現在基本實現完全自主生產。DH 公司的產品在國內外小型農機市場中以“質量過硬,價格公道,服務至上”的尚佳用戶口碑廣受全國各個地區客戶青睞,目前每年的銷售量穩定保持在 5 萬臺以上并逐漸擴增,自公司開展銷售以來已經先后服務三十萬以上客戶。
第二節 研究目的和研究意義
一、研究目的
就 DH 公司而言,日益增加的產品銷售數量和隨之增加的服務客戶數目都勢必要求 DH 公司在產品生產制造和產品售后方面相關方面增加資金投入,而在總體資金受到制約的情況下,公司就不得不考慮將利潤增長點放在了“節流”上面。而生存發展了 13 年之久的 DH 公司的生產規模也是一步步地在擴大,原有的陳舊生產規劃相對滯后,在制品的搬運浪費現象也日益突出,這也阻礙了公司生產效率的提升。同時,類似于等待浪費等浪費現象也一直始終充斥于生產的全過程之中,生產部每天的全員班前會占用時間基本為 15 到 20 分鐘,會后要想進入生產狀態,各工位的準備時間等又需要 20 分鐘以上,最長的時候準備時間長達 45分鐘。往往生產進入有序狀態,基本上需要上班后將近 1 個小時。每個生產班組八分之一的時間就這樣被白白浪費掉。為長期持久地生存發展下去,并使效益增加,減少在生產過程中各種浪費也就日趨重要。
以 DH 公司眾多產品中的一款自制件 750 鋤草輪為例進行說明,該自制件的銷售價格為 100 元,其總成本核定為 90 元,單件利潤僅為 10 元。想要實現利潤翻倍的目標有兩條實現途徑:一是在不進行生產過程優化和改善的前提下,產品單件利潤不變,只有通過將該產品的銷售量翻倍的方式來實現利潤翻倍。眾所周知,這樣的目標達成難以企及且需要投入大量營銷費用。二是將目前生產產品的總成本壓縮 10 元,通過關注和減少生產過程中的浪費問題來壓縮成本、提升產品利潤就要相對容易的多。因此,對 DH 公司生產過程中各種浪費問題進行研究及改善是毫無疑問具有其現實意義,也能夠為行業內其他企業借鑒意義,促進行業發展。通過對 DH 公司搬運浪費問題進行研究和實踐,筆者一方面能夠幫供職企業 DH 公司制定企業更合理的生產改進方案,另一方面能夠將研究所學理論聯系實踐、總結經驗后形成系統教學教材以供新進員工系統培訓使用,也可以在未來作為企業的生產指導體系核心內容長期運用。
第二章 相關理論及概念
第一節 精益生產的理論基礎
一、精益生產的來源
生產方式的相關理論大體上分為三種:第一種是泰勒的科學管理理論;第二種是戴明的質量管理理論;第三種是精益生產理論。精益生產理論起源于二戰后。美國福特汽車依靠其資源豐富、大量資金投入、大規模場地,采用批量生產模式——品種少且依托規模化而降低成本,提高競爭優勢。僅在 1949 年,美國福特單日產量達到 7000 臺,相當于日本豐田建廠之后總產量的近 3 倍。
日本的豐田汽車公司面臨著國內資源匱乏、技術落后、可用場地小等諸多困難。在豐田競爭優勢長期不足的情況下,由大野耐一建立了一套適合日本戰后基本國情的豐田管理模式,通過“一人多機”、“目視化管理”等管理方式,使豐田扭虧為盈,形成了豐田準時化生產 JIT(Just In Time)。之后被美國麻省理工學院(MIT)的教授詹姆斯.P.沃麥克總結為精益生產(Lean Production)。豐田汽車公司利用 JIT 使豐田汽車的年產量在 2014 年達到了 998 萬輛,位列當時的世界第一。
二、精益生產的概念及特征
精益生產方式是一種區別于單品種、大批量生產方式的小型化,多品種,多樣化的生產方式。與大批量生產方式相比較,精益生產方式具有準時化生產(JIT),看板管理,員工參與度高等特點。在《改變世界的機器》一書中,丹尼爾教授給精益生產定義了 5 個方面的特征:
(1)把用戶當“上帝”。 (2)以“員工”為中心,適當放權,充分發揮員工的積極主動性。 (3)精簡組織機構,盡可能多采用 JIT 和看板式管理物流,大量降低在制品和產成品庫存,減少廠內物流。 (4)培養團隊意識和并行設計。 (5)及時化準時化供貨方式。降低在制品和產成品庫存量,減少搬運頻率和廠內物流車流動頻次。
第二節 生產浪費的分類及搬運浪費定義
一、精益生產理論中生產浪費的概念及分類
企業在生產經營中活動中,不增值活動的占比最高能達到 90%以上。這就意味著只要企業正常生產運營,就會不停地發生不增值活動,而有一些不增值活動也是企業運營過程中必然會出現的[1]。 精益生產理論認為:不增值活動可以分為可以不做的作業和不得不做的作業兩種:
(1)可以不做的作業,即只增加成本而不產生附加值的活動。它們約占企業生產和經營活動 35%,是最先也是最需要改善的活動。例如,尋找、臨時儲存等。
(2)不得不做的作業,是指到目前為止還必須要完成的活動,必須伴隨著生產活動一起實施而不產生附加價值的作業。這一類約占企業生產和經營活動60%。例如,沖壓下料過程中的沖壓模具更換調整維修,機器人操作程序更改微調、為拿取工件工具而產生的走動、拆開包裝物等搬運活動。
精益生產理論認為所有的浪費均為不產生附加值的活動。對于企業來說,無論如何進行生產活動,只要所從事的活動未給企業帶來價值,未給客戶帶來價值的一切活動均能定義為浪費。因此,無論是庫存的在制品還是產成品,亦或者是呆滯品;無論是再小的瑕疵還是生產過程中可輕易修復的不良;無論是制定戰略的會議還是為了提高效率而開的生產現場會議;無論是為降低成本的計件薪酬還是各種各樣的福利……等等這一切均不會給客戶帶來直接效益,都是精益生產理論中所定義的浪費。
第三章 DH 公司生產過程搬運浪費問題現狀 ...................... 19
第一節 DH 公司的企業概況 .................................. 19
第二節 DH 公司的生產現狀 ..................................... 20
第三節 DH 公司搬運浪費問題現狀 ............................ 21
第四章 DH 公司生產過程搬運浪費問題原因分析及影響 ............. 27
第一節 DH 公司生產過程搬運浪費問題產生的總體原因 ...................... 27
第二節 DH 公司搬運浪費產生的具體原因 ................................ 28
第五章 基于精益生產理論的 DH 公司搬運浪費改善 ................ 35
第一節 生產浪費改善方案 .................................. 35
一、總裝線布局搬運浪費改善方案設計 ............................. 35
二、減速箱分總成分裝線搬運浪費方案設計.............................. 36
第五章 基于精益生產理論的 DH 公司搬運浪費改善
第一節 生產浪費改善方案
精益生產方式的根基是及時化生產(JIT)和消除浪費。面對層出不窮的浪費,要逐一進行消除。針對 DH 公司在生產過程中出現的種種浪費,公司內部也在逐步尋求解決方案,逐個解決。無論哪種原因導致的搬運浪費都是精益生產理論所不允許的。在精益生產理論中,大部分搬運活動都是不增值的活動,都是需要被消除的。限于公司目前實際狀況以及在解決現有浪費的基礎上不再產生新的浪費的情況,DH 公司本著花小錢辦大事的方針正在分批分步驟解決浪費問題。具體的方案本文以搬運浪費中的三個特別例子為對象出設計方案,并擇機實施。
在方案設計機實施過程中,在尊重事實的基礎和最大化效益的原則下,利用ECRS 做改善方案——E(Eliminate)取消,C(Combine)合并,R(Rearrange)重復,S(Simplify)簡化。在此原則之上,將不需要做的搬運流程取消,將能合并的生產線合并或將設備與設備合并在一起,避免一些重復的搬運,簡化生產流程。盡可能多的將所有可以不做的搬運浪費消除。
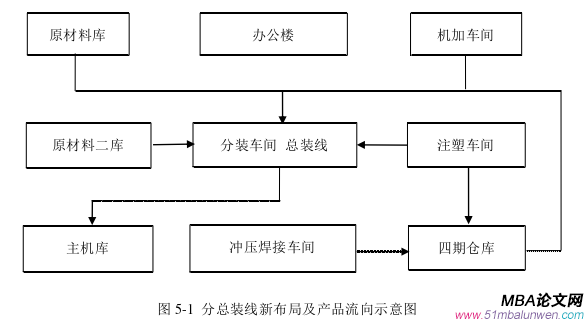
第一節 結論
通過對 DH 公司以上幾個具有代表性的零部件和流水線布局調整前后的數據分析對比不難看出,DH 公司在搬運浪費消除方面走出的路是一條積極探索的路。路的方向是正確的,是積極向前的。這三項搬運浪費在整個生產過程中十分突出。要想提高效率,好好節流,消除現有的浪費是一條必由之路。生產過程中的浪費問題在產品生產總成本中的比重之所以最高能達到 95%的最大原因在于,公司管理者習以為常的認為這些很正常,其他企業也是這樣的。這樣的想法直接導致從業者對各種浪費問題的忽略或者重視程度不夠。只有清醒地認識到浪費問題的嚴重程度,進一步通過規劃實施去消除,將消除浪費的 PDCA 不停循環的做下去,浪費問題就會逐步得到解決。
DH 公司僅僅總裝線調整一項消除搬運浪費的直接經濟效益就有六萬元,而這僅僅是基于年產五萬臺的銷量得出的數據。如果 DH 公司年產 10 臺的目標實現,由消除總裝線遷移而導致的搬運浪費所產生的直接經濟效益將翻番。而后期倉庫庫位的調整也將是消除搬運浪費問題的最大最有效途徑。少了搬運,也就省下了部分搬運方面的人力物力支出,同樣也省下了搬運設備方面的財務支出。
從 DH 公司對生產過程中搬運浪費的減少可以看出,浪費的消除或者減少直接的效應除了降低成本,也減少了一線的操作人員。使得 DH 公司向少人化又向前邁進了一步。同樣,生產過程中各種形式浪費的消除將是企業參與市場競爭的一項基本且重要的內功。修煉好此項內功,產品的競爭力必將快速提升。
DH 公司的搬運浪費改善的效果是明顯的,成果也是可值得書寫的。但對比一下改善前不難發現,我們的改善還存在很大的不足:1、還沒有把搬運浪費的改善擴大到公司的其他方面,一些半成品在車間之間的搬運,零件在設備之間的搬運;2、搬運工具的改進不只是行車這一項,升高車以及電動手拉叉車的改進,特別是手動叉車的行進速度上還有很大的空間;3、倉庫在收貨和發貨的過程中登高車的運用上面以及倉庫內庫位設置的不合理等等,4、還沒有將均衡化生產擴大到全部生產線。
參考文獻(略)
相關閱讀
- 供電作業項目安全生產風險管控系統開發及后評價研究2018-01-28
- 6S生產管理在浙江農行的應用與提升研究2018-02-01
- LY市甲醛行業安全生產多元化管理研究2018-02-13
- L公司中層生產管理人員薪酬體系優化研究2018-03-07
- DL植物工廠規模化經營生產戰略管理研究2018-03-23
- 美卓礦機機械加工件的逆向定價生產管理研究2018-04-23
- 核電數字化分布式儀控系統研制進度風險管理研究2018-05-02
- 尾砂壩加高工程和加高后安全生產管理措施的研究2018-05-15
- 武漢鐵路局漯河車站行車安全生產管理分析研究2018-05-18
- 軌道交通供電運行安全生產管理系統研究與應用2018-05-31